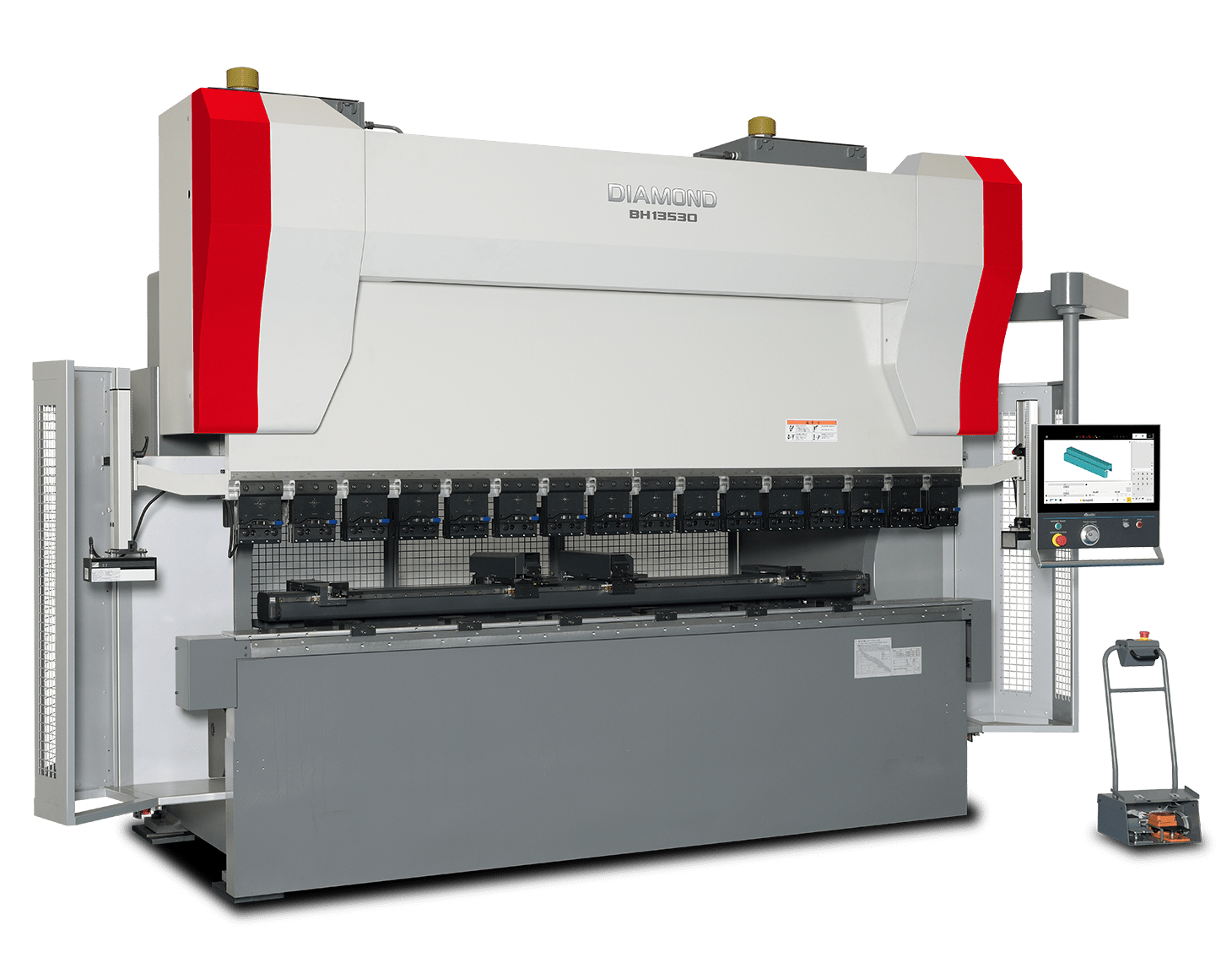
FINEST PRESS BRAKE ON THE PLANET
Diamond BB Electric Press Brakes
Fully Electric Diamond BB Press Brake
From the originators of the world’s first electric press brake, the BB Series offers solid performance and know how in bending. The BB Series ball screw press brake with 100% MITSUBISHI electronics, motors, and servo drives feature an AC Servo motor and ball screw mechanism for high-speed productivity and repeatability (± 0.001mm). When you need accuracy every time, you can count on the BB Series. The Upper Beam Drive System enables high-speed movement and incredible ram repeat-stop accuracy. The high speed, high precision back gauge has a four-micron positioning accuracy thanks to MITSUBISHI motor technology. Easy 22-inch color multi-touch screen running Windows, making programming simple and quick. Environmentally clean and quiet, the BB Series is the crown jewel of any bending department.
Design & Features
High Accuracy (±1 micron)
22” Multi-Touch LCD Control
3D Simulation
Tooling Library
World Class Productivity
28 to 55 US Tons
25 to 83 Inch Bending Length
Pulse handle with axis control & bending support
25.6” X-axis max gauge distance
(4 micron back gauge repeat accuracy) +0.004mm
CNC control with Microsoft Windows
CNC back gauge (4 or 5 axis back gauge)
LED lighting over back gauge and front work area
Diamond BH Hybrid Series Press Brakes
Diamond BH Dual Drive Hybrid Press Brake
The Diamond BH “Dual Drive” system controls high-speed up and down movement with a ball screw and bending movement by the servo-hydraulic piston. The Dual Drive System allows high-speed down-movement at 200 mm per second with high repeat-stop accuracy. In addition, the Dual Drive System offers energy savings thanks to an assist device that stores the energy of down movement and returns it during ram up movement. The ram floats on a gas cushion, thereby greatly diminishing the weight to return the ram to the top of the stroke. Accuracy is key to the BH Series. Ram cylinders powered by AC servo motor piston pumps deliver positioning accuracy unparalleled in the industry. Combined with the accuracy (4 micron) of the back gauge driven by MITSUBISHI motors every time part after part! With Automatic Thickness Detection, angular irregularities are minimized due to material thickness and off-center bending, the BH Series proves to be an amazing machine tool.
Intelligent Intuitive Control
Highly Reliable
Cost Efficient Operation
World Class Productivity
Innovative Dual Drive system
22” Multi-Touch Display
Tooling Library
Large Program Capacity (40GB)
85 - 250 US Tons
High stable repeat accuracy (1-micron repeat accuracy)
+0.001mm High-Speed Hybrid drive (Fastest cycle time in its class)
Large Stroke and Open Height
Patented Automatic Micro Wedge Crowning
Automatic Thickness Detection – On The Fly
Standard 5 axis back gauge
USB & Lan peripheral
102” -161” Bending Lengths
Design & Features
ATC ( Automatic Tool Change ) System
Diamond ATC Press Brake
The ATC brings further production increase and reduction of set-up time to the BH Dual Drive series. The TC 32 was developed by reviewing tool-changing applications in the market and bringing to the market greater variation of solutions to support customer’s goal of improved efficiency. The perfect solution for high mix low volume work in today’s modern manufacturing environment.
ATC Overview
Tool Storage & Storage Capacity - For tool storage customers now have options ranging from 32 meters (107.28’) up to 52 meters (170.60’) of tooling. Allowing the greatest variation of tooling storage ranging from high runner v openings or specialized tooling such as hemming or offset tooling.
Automated tool changing Improved - Fully automated tool setup/manipulator/tool cleaning – The TC will automatically change the tooling while the operator tends to other tasks further reducing the setup time to mere minutes. Due to the large single manipulator, larger tools are able to be picked and placed inside of tool setups to reduce setup time of similar tool staging. During the tool change process, the manipulator automatically cleans the bed surface and tooling removing an additional process seen in other TC applications.
User-Friendly Operation - Create programs offline through Diamond Bend or at the control - Allowing the greatest amount of flexibility for operators programs can be created offline or at the press brake for the ATC. The operator can choose to use the ATC when using programs or if tools are not available in the TC will wait patiently for the next job to load tooling.
The Machine Becomes the Teacher - Utilizing both the VIDERE operator support system and the ATC to automatically change the tooling it provides the ultimate solution for improved production and increased efficiency in the bending department. Supporting new operators or more seasoned brake operators with information in real-time in front of the operator while changing the tooling automatically is an unprecedented solution never offered to customers until today.
Videre Series Press Brake
Operator Support System
The VIDERE operator support system was developed to simplify press brake operations by clearly showing in front of the operator functional process information that is simple to see and effortless to understand.
Information from setup to processing is displayed in real time, real size and real location. Setup and work handling that once required a skilled operator is now simplified by VIDERE, improving productivity by reducing bending defects and eliminating non-value added steps in an operators daily machine interactions.
Virtual Training - Reduced Set-up Time - Fewer Mistakes - Improved Productivity - Machine Status
FastBend Robotic Bending Cell
The FastBEND Robotic Bending Cell is for small to medium parts and mid-to high-volume production and incorperates the Diamond BB press brake.
The FastBend Robotic Bending Cell streamlines metal fabrication by integrating advanced robotics with efficient bending technology. It offers a flexible solution for manufacturers seeking improved productivity and accuracy. Equipped with a precision robotic arm, it quickly performs complex bends on various materials, ensuring consistency and reducing manual error. The system that accommodates various part sizes and shapes, making it suitable for both prototypes and large-scale production. Additionally, it enhances operator safety by minimizing manual handling and protecting workers from moving parts while allowing supervision. The FastBend Robotic Bending Cell marks a significant advancement in metal fabrication, delivering efficiency, accuracy, and safety.
Features include:
Two large pallet stations
Re-grip
Squaring station
Tool storage
Automatic gripper-changing function